Dalla attivazione alla fotostampa degli inner
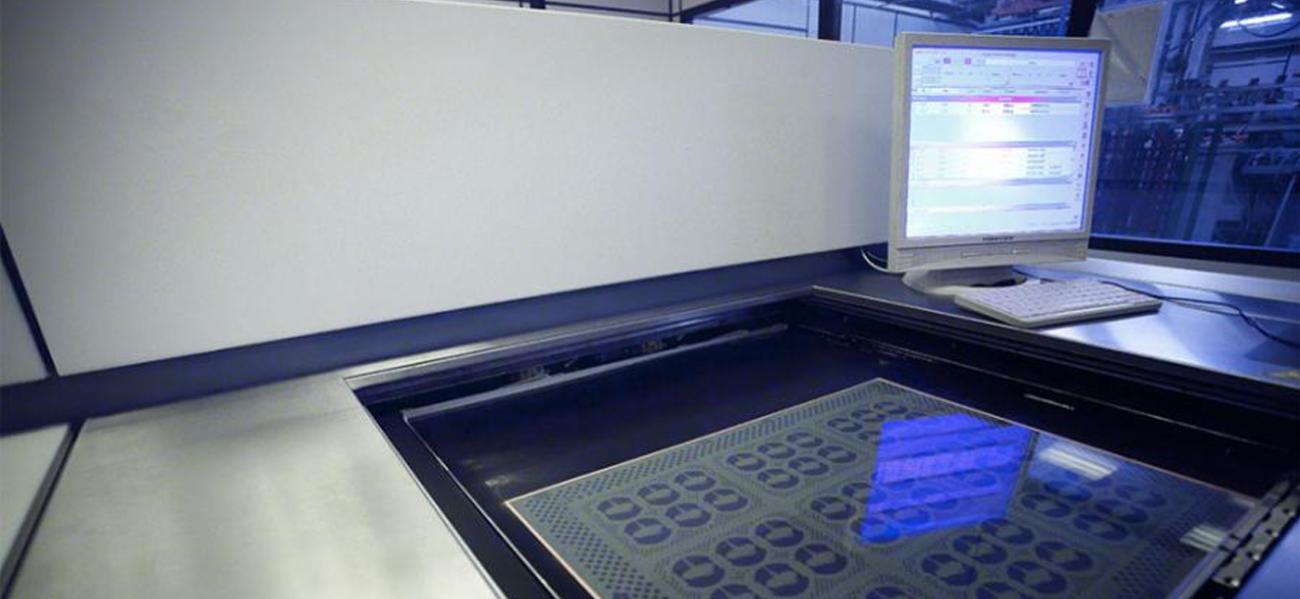
Il processo di laminazione e fotostampa
Secondo quanto riportato nel nostro primo articolo, prendendo in esame un ciclo base di un prodotto Multistrato, i processi di
1. attivazione e laminazione degli innerlayers e
2. fotostampa degli innerlayers
corrispondono ai primi due steps produttivi.
L’innerlayer rappresenta uno tra i più importanti materiali di base per la realizzazione di un PCB multistrato essendo parte integrate del build-up.
Si tratta di una lamina di spessore variabile, composto da tre strati di cui
- quello centrale è costituito da un tessuto di fibra di vetro pre-impregnato con resina termoindurente e
- i due esterni sono rappresentati da due fogli di rame.
Gli spessori, sia dello strato centrale che dei due fogli di rame esterni, possono variare in base alle esigenze di progetto e alle specifiche funzionali richieste al PCB.
Lo strato centrale degli innerlayers è generalmente FR4 (flame retardant 4) tuttavia il tipo di resina e la fibra di vetro possono avere caratteristiche diverse per conferire al circuito stampato proprietà meccaniche ed elettriche adatte alla specifica applicazione d’uso.
E’ importante sapere che materiali diversi hanno costi anche significativamente diversi e che, per questo motivo, la scelta di quali utilizzare deve essere guidata dalle effettive esigenze.
Il processo di fabbricazione dei circuiti stampati comincia dunque dalla lavorazione degli inners che vengono trattati chimicamente, vengono cioè attivate le superfici esterne di rame tramite microincisione in modo da aumentarne la rugosità e garantire una migliore adesione del dry film, una pellicola di cellulosa fotosensibile che viene applicata su ambo i lati dell’inner attraverso un processo che prende il nome di laminazione.
Anche il dry-film, può essere di diverse tipologie sulla base delle caratteristiche dello spessore del rame dell’inner utilizzato e del pistato che verrà impresso nella successiva fase di fotostampa che consiste nell’esposizione del dry-film stesso ad una sorgente di luce.
Due sono le tecniche di fotostampa:
- quella ad immagine inversa, tipica della fotografia tradizionale, e
- quella ad immagine diretta realizzata attraverso sistemi laser o led (Laser Direct Imaging e Led Direct Imaging)
Fotostampa a immagine inversa
Nel primo caso è necessario stampare il negativo del pistato previsto da gerber su una pellicola attraverso una macchina chiamata plotter. Tale pellicola verrà poi utilizzata in una macchina di fotostampa dove verrà interposta tra una fonte luminosa e il dry-film laminato sull’inner: ogni volta che la fonte luminosa emette luce il positivo del pistato viene “fotografato” sul dry-film stesso. Le caratteristiche del dry-film colpito dalla luce si modificano, diventa più resistente (di fatto polimerizza) e questo consentirà che nelle successive fasi di sviluppo (rimozione del dry-film non polimerizzato) il rame sottostante venga preservato, cioè che vengano preservate le piste di rame previste da gerber.
Tutto il dry-film sulla restante parte del pannello e il rame sottostante verranno invece rimossi in specifiche fasi che prendono il nome di
3. Dry-film development, Copper etching and dry-film stripping
Fotostampa a immagine diretta
In questo caso il dry-film viene colpito in modo selettivo a disegnare il pistato previsto da gerber o da un fascio di luce laser o da un fascio di luce led, due diverse tecnologie che sposano la stessa tecnica di imaging.
I vantaggi del “direct imaging” sono numerosi
- non è richiesta una pellicola che di fatto è un consumabile
- non è richiesto un plotter (e relativa sviluppatrice) e un tecnico capace di programmarlo oltre che di uno capace di utilizzarlo
- la pellicola è soggetta all’aging ovverossia cambia dimensioni (dilatazioni e distorsioni) nel tempo e perché questo effetto sia limitato è necessario conservarla in ambienti realizzati ad hoc con condizioni di temperatura e umidità controllata
- in ogni caso, per il motivo precedente, la pellicola deve essere periodicamente ristampata
- un errore sulla pellicola, generato da un graffio o più comunemente da una particella di polvere, si trasmette su tutti gli inners che ne hanno previsto l’uso
- la pellicola non permette adattamenti ad hoc, la stampa indiretta non permette correzioni basate sulle distorsioni di ogni singolo inner
La stampa inversa tradizionale è stata dunque superata dalle tecnologie di direct imaging che, in aggiunta, consente di garantire con precisone massima la realizzazione di piste e isolamenti di spessori significativamente inferiori, anche al di sotto dei 50 micron.
Proseguiremo con i prossimi articoli nella descrizione del processo, ci limitiamo ora a far osservare che soltanto in queste prime fasi abbiamo già introdotto nozioni relative a materiali di base, di chimica organica e inorganica oltre che di fotostampa per spigare quante e quanto profonde debbano essere le conoscenze per operare nella produzione dei circuiti stampati.
E’ inoltre necessario mettere in evidenza che l’accelerazione nello sviluppo delle performance richieste ai dispositivi elettronici ha imposto analoga accelerazione nello sviluppo delle tecnologie di produzione.
Pertanto, è necessario disporre non solo di numerosi macchinari ma che essi siano sempre aggiornati alle più recenti tecnologie.
Chi si ferma è perduto!