Il ruolo dei materiali di base nei circuiti ad alta prestazione
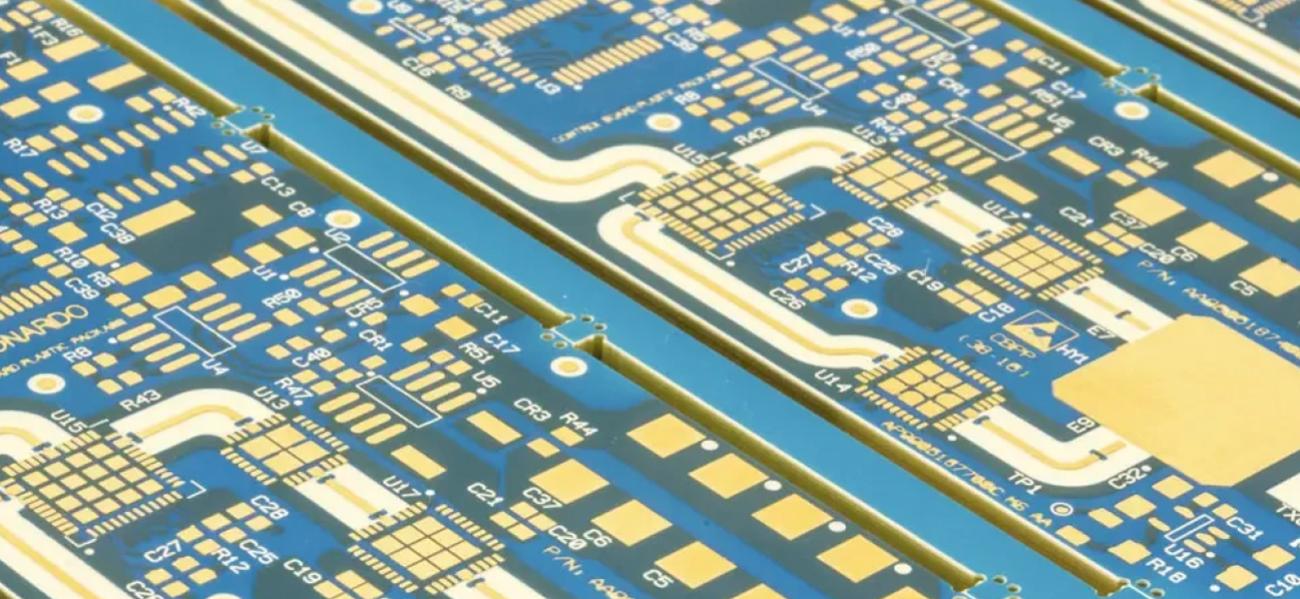
I materiali di base, e i laminati in particolare, stanno acquisendo una notevole importanza nei circuiti ad alte prestazioni; le basse perdite (low losses) così come la costante dielettrica bassa (o costante dielettrica costante) sono aspetti critici nella formazione dei laminati.
Per i processi di assemblaggio senza piombo è necessaria una maggiore resistenza al calore: i laminati che necessitano di resistere ad alte temperature devono avere una maggiore Temperatura di Decomposizione (detta Td).
Altre caratteristiche importanti per laminati sono:
- distribuzione uniforme del vetro per avere una qualità migliore nella foratura laser
- tessuti di vetro più sottili per avere proprietà elettriche migliori
- dielettrici più sottili per una capacità distribuita tra l’alimentazione e la messa a terra.
Sta, inoltre, via via ampliandosi la gamma dei laminati per la realizzazione di componenti incorporati quali resistori e/o condensatori.
I nuovi laminati, progettati per circuiti ad alte prestazioni, devono essere rivisti per quanto riguarda gli aspetti termo-meccanici ed elettrici.
Qui di seguito una lista delle caratteristiche da prendere in considerazione durante la fase di scelta dei materiali.
La scelta dei materiali
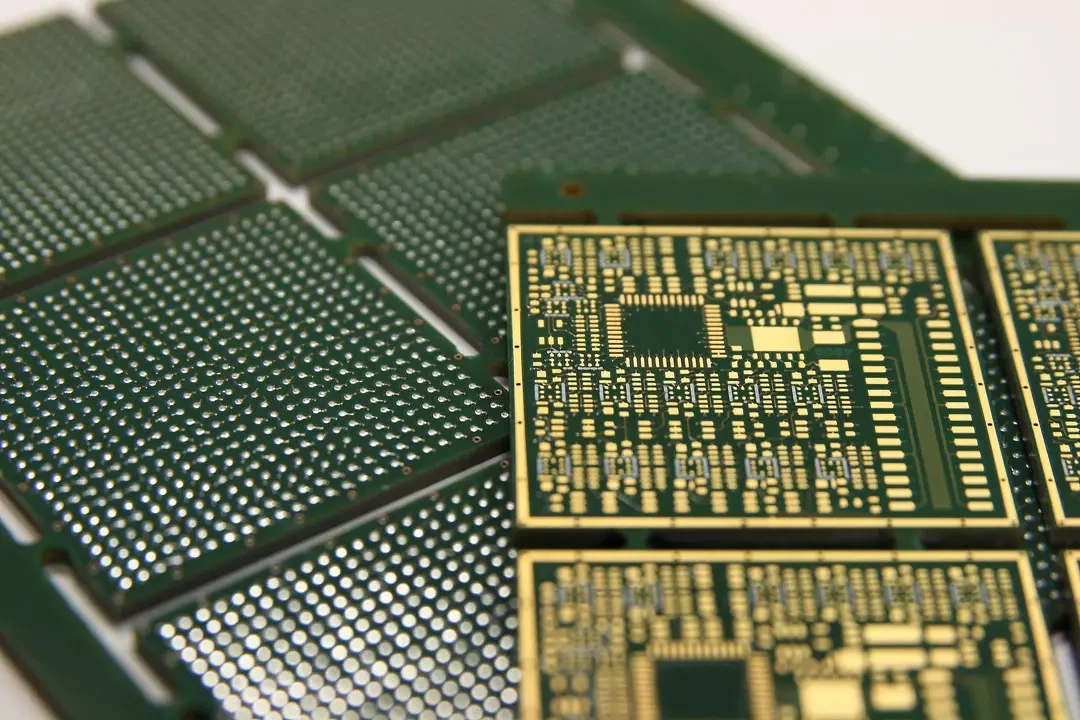
CTE
Espansione termica sugli assi x, y e z con particolare riguardo all’asse z per l’affidabilità dei vias (ad esempio barrel cracking) e resistenza ai molteplici processi di pressatura.
Perdita tangente (Df) e permittività (Dk)
Parametri per l’integrità del segnale e requisiti dell’impedenza.
Tipo di vetro e contenuto della resina
La distribuzione uniforme del vetro aiuta a migliorare la qualità della foratura laser
I tessuti di vetro più sottili aiutano ad avere proprietà elettriche migliori
I dielettrici sottili rendono possibile avere una migliore distribuzione della capacità tra l’alimentazione e la messa a terra.
Temperatura di transizione vetrosa Tg
La temperatura alla quale il materiale smette di comportarsi come un materiale rigido.
Temperatura di decomposizione Td
Per i processi di assemblaggio senza piombo è necessaria una maggiore resistenza al calore: i laminati che devono resistere ad alte temperature devono avere una temperatura di decomposizione più elevata (Td). Si tratta della temperatura che il laminato può tollerare quando ha perso il 5% del suo peso mediante analisi gravimetrica termica (TGA).
Impatto dell’umidità sul prodotto finale
Aspetti fondamentali possono essere la resistenza del filamento anodico conduttivo (CAF) e l’assorbimento dell’umidità.
Impatto ambientale
Necessità di laminati a basso contenuto di alogeni ("Low Halogen”) per l’elettronica sostenibile.
I tuoi bisogni, la nostra competenza
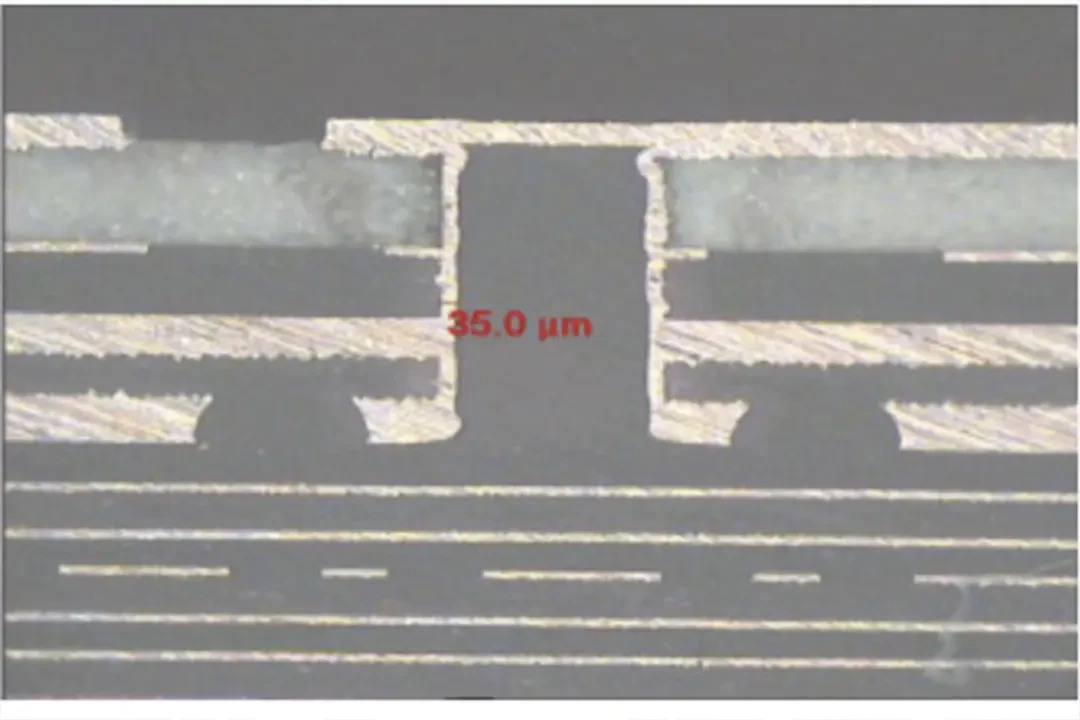
Tutti i materiali validati utilizzati da Cistelaier sono elencati qui di seguito, in corsivo quelli specifici per circuiti ad elevate prestazioni.
FR4 standard, laminati ad alta Tg anche senza alogeni e specifici per il digitale ad alta velocità:
- FR4 standard e senza piombo: Iteq IT140 e IT588; Isola Duraver ML104i - Tg 140 °C;
- FR4 NeroEpossidico a media Tg per processi senza piombo: Iteq IT158 -Tg 160 °C; Isola IS400 -Tg 150 °CSenza alogeni a media Tg: Iteq IT40G -Tg 140 °C, IT150G
- Epossidico ad alta Tg 180°C (senza filler):Iteq IT180 (anche senza/a basso Prepreg); Isola IS420e IS410; ARLON 45N
- Epossidico ad alta Tg 180°C (con filler): Iteq IT180A e IT180i; Isola PCL370HR;Nelco N4000-29;Hitachi 700GR; EMC 827 i
- Epossidico ad alta Tg 170°C – senza alogeni: Iteq IT170GRA1 e IT170G e IT180GN
- Applicazioni ad alta velocità: Nelco N4000-13(Si) e N4800-20(Si); Isola Fr408HR, IS600(serie), Astra e I-Tera; Iteq IT200DK e IT150DA(SE), IT-968 (SE), IT-988G, IT-988G SE; Panasonic Megtron6 e Megtron7
- Capacitance layer: OAK-Mitsui Faradflex
Materiali ad alte prestazioni per applicazioni avionico/militari:
- Sistema con resina Polyimide: Arlon 33N, 35N, 84N, 85N, 85HP; Ventec VT901(anche senza/basso flow); Hitachi MCL-I-671; Isola 95P/96P; NELTEC N 7000VO
- Sistema con resina epossidica: Arlon® Kevlar 4NK (Tg 170 °C e 4.7 ppm/°C)
- Thermount® epossidico e Polyimide e fibra Para Aramid: ARLON 55NT/85NT
- Copper/Invar/Copper: tipicamente spesso 150 ?m - 17/120/17 ?m)
- Spessore del rame: fino a 500 micron e oltre, per applicazioni BusBar e tecnologia inlay&coin
Substrati per circuiti flessibili:
- Laminati flessibili – a base di film in Polyimide: DuPont PYRALUX LF; PYRALUX FR
- Laminati flessibili – a base di film in Polyimide senza adesivo: PYRALUX AP, PYRALUX AP-Plus e PYRALUX TK
- Laminati flessibili – a base di Polyimide senza adesivo: UBE Upilex; Iteq IF-2LD; Panasonic Felios
- Strato di schermatura Emi: Tatsuta SF-PC6000 e TATSUTA SF-PC 3300
Materiali ad alta frequenza a base di Teflon® e non:
- Rogers® / Arlon (anche supportati da rame/ottone): RT/Duroid Family; RO3000 Family; TMM Family; DiClad Family; Isoclad Family; Cuclad Family; AD Family; AR Family; TC Family
- Rogers® / Arlon®: RO4350 e RO4003 (materiali di back up per materiali fuori produzione 25N e 25FR, parzialmente applicabili)
- Rogers®: ULTRALAM® 3850HT – Polimero Cristallino Liquido (LCP)
- Materiale Iteq "di nuova generazione” per applicazioni RF e Microvawe: IT-88GMW, IT-8300GA, IT-8338G, IT-8338A, IT-8350G, IT-8350A, IT-8615G with Dk da 3,00 fino a 6,15(,05)
- Taconic®: RF25A2, RF35, RF35A2, RF45, RF60, TSM-DS3, Cer10, FastRise, TACLAM Plus e tutta la famiglia Teflon® (TLX, TLY, TLE)
- Nelco: serie Mercurywave, Meteorwave (serie 1000 e 4000) e tutta la famiglia Teflon®
- Foam: Rohacel HF51